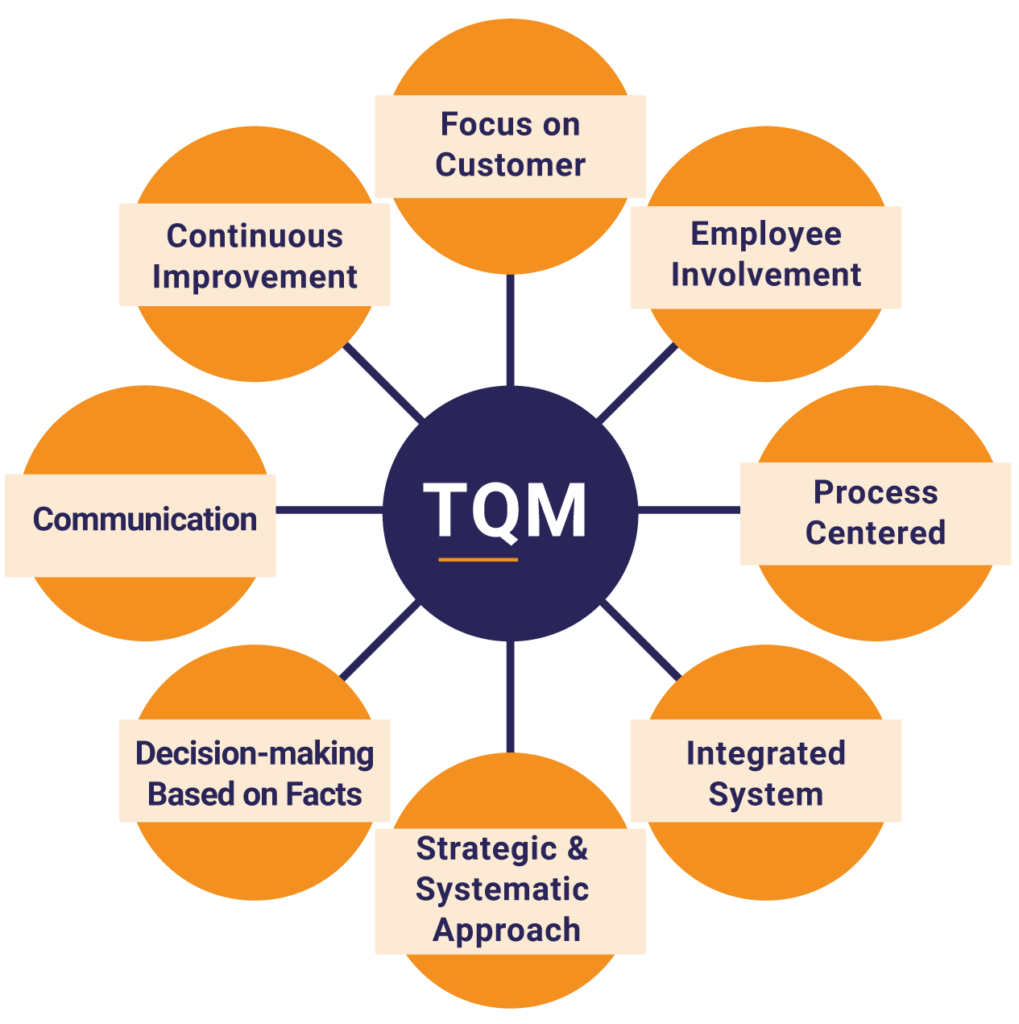
TQM is the form of statistical quality control that was invented by Walter A. Shewhart in 1930s. It was initially implemented at Western Electric Company, in the form developed by Joseph Juran who had worked there with the method. The history of total quality management (TQM) began initially as a term coined by the Naval Air Systems Command to describe its Japanese-style management approach for quality improvement. An umbrella methodology for continually improving the quality of all processes, it draws on knowledge of the principles and practices of the behavioral sciences, the analysis of quantitative and non-quantitative data.
In 1950s W. Edward Deming taught methods for statistical analysis and control of quality to Japanese engineers and executives. This can be considered the origin of TQM. Joseph M. Juran taught the concepts of controlling quality and managerial breakthrough. Authors Armand V. Feigenbaum and Philip B. Crosby have written books on TQM named “The power of Management Innovation” and “Zero Defects Thinkers” both books paved the way for quality improvement in many companies. In 1968 the Japanese named their approach to total quality “companywide quality control.” It is around this time that the term quality management system became famous. Kaoru Ishikawa’s work on the philosophy of TQM contributed to Japan’s dominance as a quality leader.
Today TQM is the name for the philosophy of company broads and complete approach for managing organizational quality. TQM and the Six Sigma management strategies are similar; TQM focuses on the feedback and Six Sigma focuses on elimination of defects or errors. TQM is often referred to as a Business Excellence Model. Since TQM has worked so well at such a wide variety of organisations, there are several models in place throughout the world, each with minor modifications suitable to the organizational practice. However, it is worth noting that the practice focuses on the operation and application of information obtained via feedback from all related sources.
Companies such as Ford Motors, Toyota, Motorola, Xerox Corporation use TQM. These corporations have witnessed how TQM has helped them to focus on the customer, while deepening customer loyalty. Profits increase easily because the cost of attracting a new customer is so much higher than the cost of retaining an existing customer. When customers realise that their opinions matter and that the company responds to their feedback, they feel valued and their assessment of the organisation rises.
However, moving to a TQM methodology requires time and training, which represents a cost to the company. In early iterations, TQM training was given throughout the organisation. Many companies have pulled back from this strategy, extending TQM training only to employees who will have the ability to gather feedback or who have a direct stake in the product or service.
Toyota is renowned for its lean production system and is the tenth most important company in the world according to Fortune Global 500 and one of the only companies on the list to directly address TQM. The Industrial Revolution marked a turning-point in the manufacturing industries across the world with the introduction of assembly-lines and mass production. The process required innovation and revolution in which Japan always topped. Another turning-point came during the Second World War. Weapon-manufacturing, especially in the U.S., required the optimization of manufacturing machinery, goods and statistical methods to keep track of production, so it went in for TQM. Although the U.S. took part in the development of Quality Control methods, industrial engineers and statisticians who wanted to implement new techniques were often overlooked because Quality was associated with a greater effort and restrictive regulations.
Japan’s economy was devastated in World War II. All the large cities with the exception of Kyoto, the industries and the transportation networks were severely damaged. Japan required economic rebuilding; therefore they invited statisticians and quality managers such as Edward Deming and Malcolm Badridge to help restructure the economy. Toyota was one of the first companies to implement Quality Control in the 1940’s and 1950’s. Toyota’s current method known as “lean production” owes itself to the work of Edward Deming and is today a reference point for Quality Management worldwide.
Kaizen is a part of TQM and it refers to continuous improvement. The definition of kaizen comes from two Japanese words: ‘kai’ meaning ‘change’ and ‘zen’ meaning ‘good’. Kaizen philosophy was first introduced by Toyota back in the 1980s and has since been adopted by thousands of companies around the globe. This lean transformation encourages an improvement in culture that gradually increases quality, efficiency, and profitability. Kaizen is a statistical process that controls and improves quality in every aspect of business processes. Employees are empowered to suggest ideas that address common problems so that they don’t reoccur. By tackling issues right in time, they are not allowed to persist and grow into bigger challenges. This grassroot approach has transformed into lean digital transformation, saving frontline employee’s precious time and empowering them at the same time.
Toyota’s system ‘the Toyota way’ is based on continuous improvement simultaneously eliminating waste. It respects and values the employee participation highly. There is constant encouragement for further innovation, consensus and ideas for improvement. The Toyota Way focuses on long-term improvements rather than short-term. The main pillars of the Toyota Way are ‘Customer First’, ‘Respect for People’, ‘Systematic Approach to Management’, ‘Factual Approach to Decision Making’, ‘Mutually Beneficial Supplier Relations’, ‘Process Involvement’, ‘Leadership’ and ‘ People Involvement’.
TQM’s ultimate goal is to foster customer loyalty by delivering service that will keep customers’ purchases repeating. TQM strategy works only on consistent feedback from employees and customers.